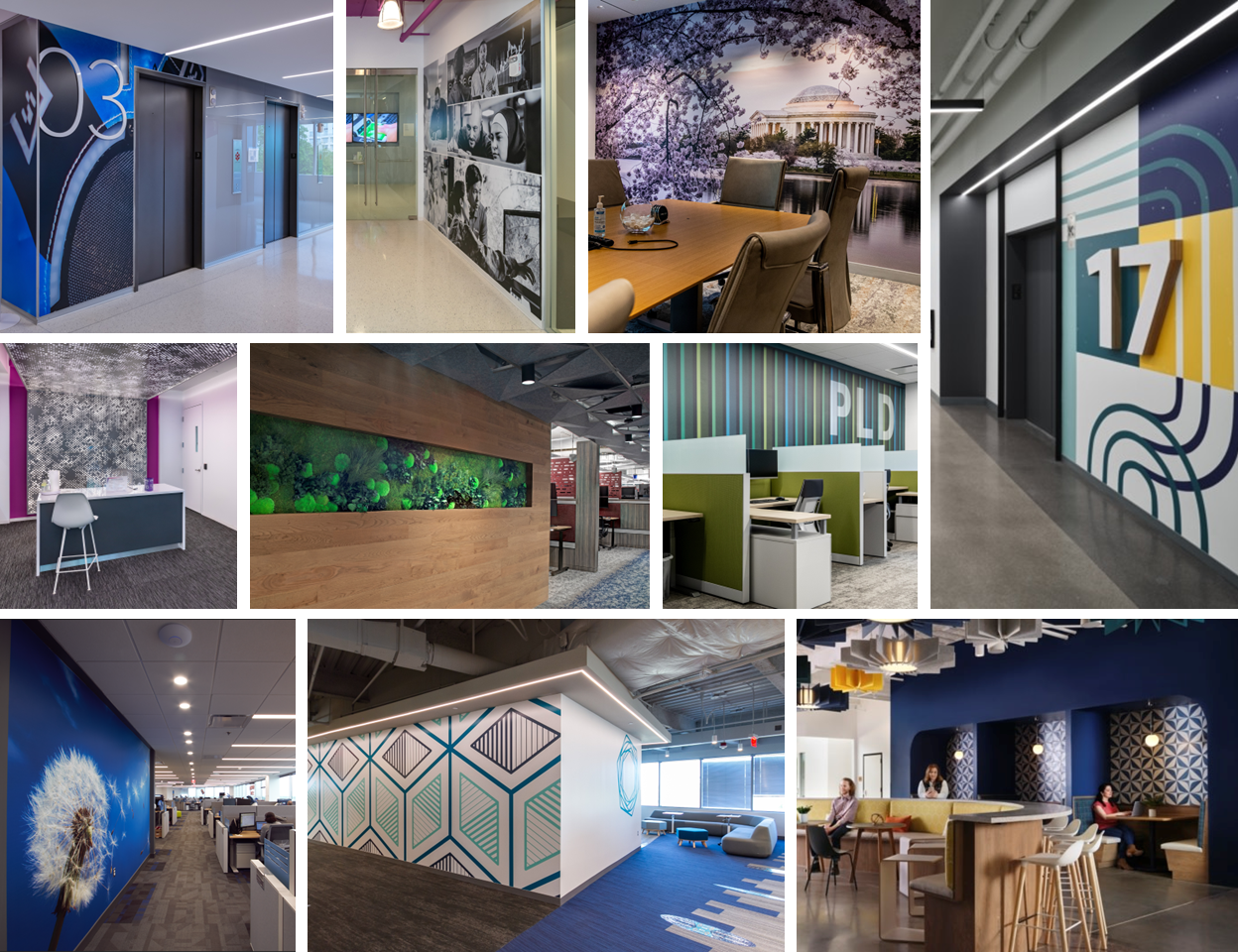
Pro Design Tips for Office Interiors: Accent Walls
April 14, 2025
Samantha Butcher, Senior Interior Designer at Arium AE, shares some of the top tips for accent walls in today’s office interiors. Continue Reading
Samantha Butcher, Senior Interior Designer at Arium AE, shares some of the top tips for accent walls in today’s office interiors. Continue Reading
Arium AE provided full architecture and MEP engineering design services for the shell and interior fit-out of Titan Steel Corporation’s new manufacturing plant in Baltimore, Maryland. The 100,000-square-foot tilt-up concrete warehouse is the fifth Arium AE has designed at the Hollander Business Park for FRP Development. The Hollander Business Park is a 50-acre planned industrial park just 4.7 miles from the Port of Baltimore, the farthest inland port on the East Coast.
After 75 years in the same Baltimore location, Titan Steel Corporation needed to relocate. The steel and aluminum core product manufacturer for clients worldwide selected a site in Hollander Business Park. Arium assisted with the site selection through the referral of mutual clients. Even though the speculative warehouse already in design with FRP would be appropriate for most distribution uses, the pivot to Titan Steel would require significant design modifications. Because of Arium AE’s integrated design team and creative solutions, we were able to quickly make the tenant-specific revisions and keep the project on track for permit and construction.
Extra thick metal fiber reinforced slabs were used to offset the extreme weight of Titan’s massive equipment, including pieces dating back to the 1950s. Custom elements, such as drive-in truck bays for loading and off-loading steel pallets, were added to the design. Arium did numerous surveys to determine power, gas, and air requirements to ensure they had a plug-and-play plan. The manufacturer could power up and start work as soon as the equipment was installed in the new space.
Structural Engineer: Tarantino Engineering Consultants
Civil: Baltimore Land Design Group, Inc.
Construction: FRP Development
Arium AE served as the Architect and MEP Engineer for the construction of a two-story, 140,000 sq. ft. high-tech manufacturing facility in Germantown, Maryland. This facility balances the design aesthetics of the surrounding innovation park with the practical needs of a high-tech electronics manufacturing and research facility. The envelope is defined by spectral cantilevered wall features and insulated tilt-up concrete panels adorned with a random stone pattern. Facade depth is achieved through layers of artistically applied stain. This facility will provide students with academic and career advancement opportunities through a partnership between the manufacturer and the adjacent community college.
Arium also completed the full design of the complex interior fit-out, starting with a stunning reception area for employees and visitors to the facility. The entire 2nd floor provides additional office capacity, expanding on their previous facility, including large conference rooms, a main break area, and collaboration support booths. The program for the manufacturing floor required a very detailed-oriented approach when laying out adjacencies on the floor plan. Thousands of pieces of equipment along the processing lines were each meticulously accounted for to achieve adequate power, exhaust, and specialty process hook-ups. Early in the design stage, Arium visited the previous facility multiple weeks in a row to survey each piece of existing equipment that, in some cases, was 50+ years old without any available documentation. During this process, Arium worked closely with the operations team to help detail the requirements planned for the new facility to accomplish a successful move. The geometry of this build-to-suit facility placed the shipping docks on one end of the building and receiving docks on the opposite, while high bay racking storage for raw materials and products is conveniently located in between. The overall goal of the interior fit-out design was to improve upon the space and infrastructure challenges presented at the old facility to the end user and to design a flexible space to accommodate changing manufacturing needs.
The MEP (Mechanical, Electrical, Plumbing) design for the manufacturing facility was carefully crafted to meet the client’s specific needs, with a primary focus on creating lab-grade manufacturing areas. The design included a new electrical service to support the manufacturing process and a flexible busway distribution system for efficient and effective power distribution throughout the manufacturing floor. The design also considered the sensitive electronic manufacturing systems that would be used in the facility and included generator-backed UPS (uninterruptible power supply) systems for the data center. This provides a reliable and secure backup power source to ensure the data center is always up and running, even during a power outage.
After occupancy in early 2024, Arium provided assistance to support the manufacturing facility’s continued growth as process lines changed to accommodate evolving business goals. To maintain the stringent temperature and humidity requirements, the systems have been continuously balanced based on the fluid nature of operations. The end-user has requested Arium to provide additional design assistance for multiple upcoming projects to advance the business.
Structural Engineer: Tarantino Engineering Consultants
Construction: Whiting-Turner
Photos: Alain Jaramillo
Arium provided full architecture and MEP engineering design services for extensive renovations to a natural and organic pet treat manufacturing facility in Westminister, MD. The project allowed a dry ingredient processing facility to scale up into a large-scale facility that incorporated raw meat processing. The project included a large freezer/cooler building addition, meat processing area, sanitation rooms, 3-60′ industrial dehydrators, and equipment washrooms. Careful attention was paid to creating separate raw and processed side operations. This allowed for raw ingredient and prep employees to remain separated from the finished products. Throughout the design, Arium communicated and coordinated the flow of people and materials through the facility to ensure safe and efficient operations.
The design team communicated the progress and features of the design by developing a 3D model of the entire facility.
After over 50 years in use as an RV & Camping Center, this two-story structure went under a complete exterior and interior renovation. Arium provided full architecture and MEP engineering design services for the new home of Exclusive Motorcars. It features a beautiful new vehicle showroom and sales floor, upstairs office space, and photo, wash, detail, and garage service bays. The site has ample parking for a large stock of pre-owned luxury vehicles.
Arium partnered with the general contractor, KasCon, in a collaborative design-build effort to work through a host of design challenges in the adaptive reuse of this facility. At the outset of this project, the client placed a strong emphasis on transforming the lacking street presence of the existing prefabricated metal building. Arium’s design studio focused on juxtaposing various layers of materials and textures in a way that would provide a clean, modern façade at a scale that was appropriate to capture the attention of vehicles passing by on Liberty Road. The design team collaborated with the client and the contractor to develop a project that met the project’s evolving schedule and budget requirements.
In 2011, FRP Development Corporation (FRP) purchased the foreclosed property, later known as Hollander 95 Business Park, that straddled the Baltimore City and Baltimore County line. Arium was contracted to work with FRP to develop the Lot 40 parcel for a new spec warehouse. Since then, Arium has continued to provide design services for multiple Lots, including Lots 40, 41, 35, and 36.
Lot 40, the Hollander 95 Business Park, had multiple challenges to bring the site into compliance with new regulations of the Baltimore City Green Building Design Standards. From the start of design, Arium and FRP worked closely with the City to complete the design and construct a shell warehouse that met all the requirements.
During the design and construction process, FRP was approached by another Baltimore business, Up to Date Laundry, that wanted to relocate their business to Baltimore County. FRP saw this as a fantastic opportunity to sell the Hollander development to them. It was a way that the City could keep a large business, and the tenant could move into a state-of-the-art facility for their heavy industrial use. Arium provided full AE design services for the 80,000 SF production warehouse with large equipment and complex systems. The project was granted the Baltimore City Green Building Design Standards, LEED Silver certification.